Specific sectors such and pharmaceuticals and food demand the most stringent controls to ensure that the containers their products use are of the highest possible quality, but also to increase efficiency, reduce wastage and minimise downtime. The collaboration between SMARTSKIN and SCHOTT does just that – using patented pressure-sensitive skin technology.
![]() | ![]() |
SMARTSKIN TECHNOLOGIES – PRESSURE-SENSITIVE SKIN TECHNOLOGY
SMARTSKIN Technologies is a technology development company with headquarters in Fredericton, New Brunswick, Canada. SMARTSKIN has developed and commercialised the patented Quantifeel pressure-sensitive skin technology that is aimed at a variety of applications.
SMARTSKIN supports some of the worlds largest brands and their technology is leveraged by customers in over 25 countries across the globe. The SMARTSKIN team has extensive experience within the manufacturing, pharmaceutical and food and beverage packing industries.
SMARTSKIN Technologies provides a state-of-the-art system for measuring line pressure and 3D orientation in glass, can, PET, and many secondary and tertiary packaging lines. By embedding the Quantifeel™ sensor into a line, the dynamic effect of pressure and movement exerted on the device can be observed in real-time and analysed to understand the effect operational parameters have on line performance, improving efficiency, reducing wastage and minimizing downtime.
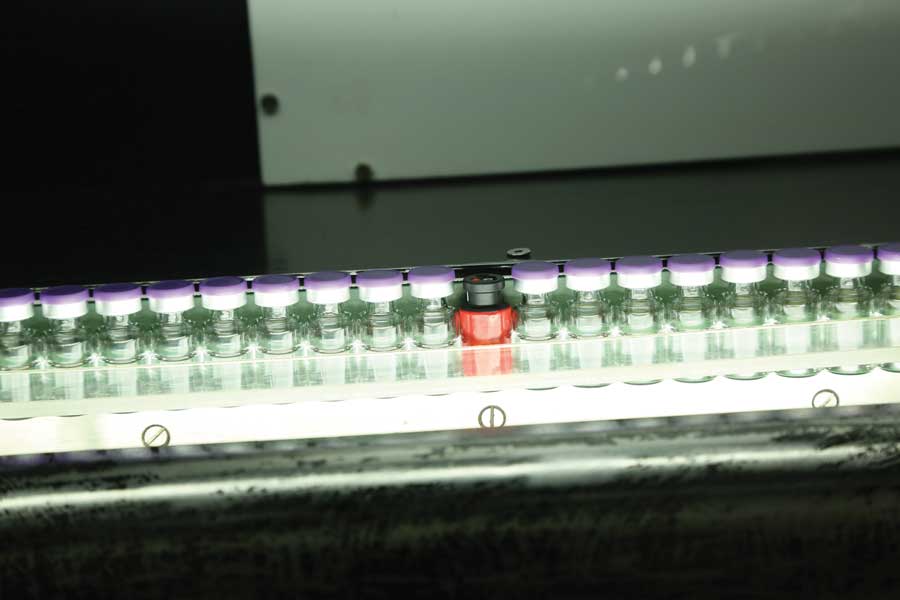
point out any parts of the line that might be applying damaging forces to the vials.
THE FILL & FINISH CHALLENGE AND SOLUTION
Fill & Finish is the core of the pharmaceutical industry. Any interference of the production process causes trouble in delivering the drug on time in a flexible and easy way. For this, it is indispensable to know what is happening on production lines and what impact they have on primary packaging. Data can be a valuable source of gaining insights on the performance of lines as well as a helpful result of ‘pain points’ of lines and primary packaging containers.
Optimising the line performance is the ultimate goal to be reached in order to deliver drugs to the people who need them the most. And what can be measured, can be managed. And what can be managed, can be optimised. The strategic cooperation between SCHOTT and SMARTSKIN optimises Fill & Finish performance at customers’ lines, reducing glass breakage, bruising and micro fractures.
SPEAKING TO SMARTSKIN
Glass Machinery Plants & Accessories (GMP&A): You are defined as a ‘Big Data Expert’ but what does that mean for the glass industry? How does it fit in with glassmaking?
SMARTSKIN: The importance of pharmaceutical packaging performance and quality for an injectable substance is paramount. There is a reason why companies put their trust in long-term suppliers like SCHOTT for their packaging needs: They need top level, unwavering quality. However, no matter how perfect the glass supply, mistakes can occur in the fill & finish process, and a cracked cartridge or a vial with particulate residue that makes it to the patient can have severe consequences.
The industry has certainly minimized this risk with improved equipment design and an intense focus on inspection and quality auditing technologies. In reality, it’s actually incredibly rare for a defect to make it out of one of these facilities and into a patient’s hands. However, when we looked at the costs for running these quality systems (yield loss, downtime, human resources), we realised they were incredibly high.
Almost all mitigation measures in place today are responsive, meaning they come with a cost of lost profits. We felt the root cause for this was a bit of a black hole: a complete absence of data around understanding the forces containers experience in a filling line. It’s like Peter Drucker said, “What gets measured, gets managed”. Suppliers couldn’t measure the forces on the containers so they had no objective way to manage and affect the process. The only element that was able to be measured was how many defects they were seeing and suppliers had to ensure these containers didn’t make it out the door. They couldn’t prevent the problem, only respond to it. This is the problem SMARTSKIN solves. Think of it like adding a “sixth sense” that allows pharmaceutical manufacturers to “see” the abuse their containers are taking and then correct it before it results in losses.
SMARTSKIN’s electronic sensor drones are IoT devices designed to mimic an actual container format and measure thousands of data points a second for multiple variables like squeeze forces, impacts, rotation, tilt, and vibration. We even have sensor products that measure environmental variables like humidity, light, or atmospheric gas concentrations. It could be a glass vial, syringe, cartridge, or even an auto injection device, but in all cases, the process is similar…These devices are inserted in the fill & finish line and automatically stream the data wirelessly in real-time as they pass through each equipment stage. We enable data collection and understanding with our software suite called Quantifeel™ that can map the process to show these adverse forces events when the line is being set up and even running at full speed. When you apply advanced analytics and cloud data processing techniques it allows comparison of like equipment across an entire organization. At that point, we can easily see what the baseline is for this type of machine and which ones require setup modification or maintenance.
It’s interesting that some have called SMARTSKIN “big data”. I guess we are in a way, but “big data” is a “BIG” space. Our vision is much more focused. With our latest advancements, we have built an AI-based condition monitoring solution around our proprietary IoT sensor drone devices. What’s different about SMARTSKIN is not just the nature of the data we enable, but also how we are applying it in a laser focused way to solve immediate problems. Many talk about the “promise” of IOT and AI, and we are among the few that can show concrete results about this promise. Our solutions allow more products to go out the door, resulting in extra profits and more importantly, extra doses for patients that need them.

GMP&A: Having SCHOTT as your leading investor is quite an important step. How does this affect your R&D and resulting technologies in terms of collaboration and ‘exchange’ of know-how? What has changed for you over these past two years since the investment came about?
SMARTSKIN: SCHOTT is a globally respected supplier of pharma packaging and services in the industry, and their expertise in glass and other high tech materials goes back over 130 years. SCHOTT is also closely connected to their customers and strives to solve the issues they are facing. For this reason, their advice is extremely valuable when it comes to aligning our development pipeline with the needs of customers.
The partnership is successful because we share a common goal to help the filling, inspection, and packaging of parenteral drugs safely and effectively deliver treatments to patients. SCHOTT makes the highest quality glass, and SMARTSKIN optimizes fill & finish operations and ensures the equipment is set
up to handle it properly.
Together we have curated a straightforward approach and the industry seemed to take notice and respond right away. There is no question the partnership has catapulted our company into the discussion of “just-do-it” technologies.
GMP&A: An important question concerns the name SMARTSKIN. You explain that it is: patented sensor drone technology that mimics the shape of vials, cartridges, and syringes paired with data mining software. But what does this mean and how does it identify problems and weak points in packaging production?
SMARTSKIN: The surface of SMARTSKIN’s sensor drones have an active, electronic “skin” or outer layer that measures force events, showing how much and the location of the force. That’s the “SMART-SKIN”. This unique data, layered with impact, vibration and rotational data, helps to pinpoint hot spots on the line that need improvement. With this new data set, technicians and engineers can confirm the improvement has resolved the issue, or if more line adjustments are required. It could be as simple as turning a screwdriver ½ turn and measuring that the pressure on the vial was reduced 30 per cent. When done as part of a normal setup check, this overall process can virtually eliminate imperfections and damage to containers, breakage, and quality investigations at their sites. It is worth millions per year in OEE for some lines.
GMP&A: What can you tell us about your Quantifeel System software? What does the use of this system involve for glassmakers?
SMARTSKIN: SMARTSKIN’s electronic drones send its data to the Quantifeel™ software platform, where the data is displayed real time and recorded, along with a suite of tools for reporting and analysis. We have placed a strong emphasis on making the data visually meaningful to the user but we feel we have only scratched the surface of what can be learned. The Quantifeel™ system enables data never before seen, and lots of it. As our user base grows, we are spending more time looking deeper into the data and machine learning capabilities, which is leading us into the area of automated anomaly detection and process insight.
GMP&A: What are your goals for the near future in terms of developments and growth? Are you considering other sectors of container glass manufacturing such as bottles and special-shaped containers?
SMARTSKIN: Our pharma customers continue to pull our Quantifeel™ technology into new applications in filling, packaging, cold chain storage, and logistics/transportation. We also support the digitalization of parenteral manufacturing lines with several soon-to-be released products. I think it is fair to say that we are positioned to become the dominant IoT platform on pharmaceutical filling lines, and strive to be an industry standard.
SMARTSKIN also works with several other industries outside pharma. We got our start in, and continue to supply and service the food & beverage industry using many elements of the same platform. We have built systems for ketchup and mayonnaise containers, juice, soft drink and beer packaging, with some very unique shapes and requirements. Our Quantifeel ProSeam™ drone, for example, enables data to be measured in filling and seaming cans at high speeds, where a soft can and high force events can cause can wrinkles, and later on, can cause leaking during the distribution phase to stores.
Our experience across multiple industries often leads to new ideas and innovations that we might not have thought of had we not had experience in that industry. So, it continues to be a nice complement to what has become our core pharma business.
Smart Skin Technologies
smartskintech.com