Carglass®, the international specialist for replacing vehicle glass in original quality, installed ISRA’s proven industrial LABSCAN system at its laboratory in Hasselt, Belgium. The information gained from optical measurements allow the company to keep high both product quality and customer satisfaction.
The challenge
Perfect optical transmission can be a decisive factor when it comes to customer satisfaction with vehicle glass. Distorting glass panes can cause the driver’s eyes to become tired and lead to headaches on long journeys. Camera and sensor-based driver aid systems also require a defined and repeatable optical glass quality.
Carglass® sees the supply of high quality vehicle glass from their suppliers as one of the main differentiators in their customer satisfaction efforts. Therefore, Carglass® requires the manufacturers to provide only vehicle glass that is cut exactly to their specification.
The solution
Carglass® installed the LABSCAN system at its laboratory in Hasselt. “Every day, we perform inspections on customer orders and check the glass from several manufacturers. This helps us adjust and constantly improve our specifications,” said Cedric Clerx, Quality Manager at Carglass®.
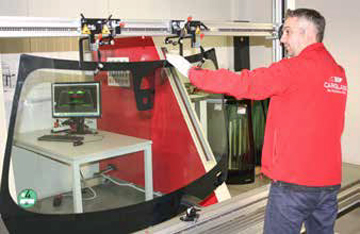
LABSCAN
- Reliable and repeatable measurement of transmitted distortion instead of subjective visual method
- Offline sample testing or process control at production sites
- Supports R&D at quality centres
- Quick and easy visualization of results, user friendly operation
- Certified by well-known global car manufacturers for compliance with their technical specifications
- Based on patented technology designed to meet global industry standards
LABSCAN at Carglass®
In training sessions held at Carglass® and the ISRA VISION Academy, users were instructed on how to professionally use the measurement system. Alongside other measures, the use of this LABSCAN measurement technology in particular represents a big step forward in terms of improving product quality and installation efficiency.
“We strive for continuous quality improvements, so that installers in our workshops can offer customers a perfect product that can be quickly and precisely installed,” added Clerx. “This is therefore an important step towards keeping Carglass®’ reliability promise to its customers.”

Summary
LABSCAN provides a wide range of options for highly customized measurements. Its flexible filter settings allow of individually adjusted measurements of all glass types. The system features integrated functions for excellent process optimization and quality monitoring. In accordance with international standards, users can also define select areas to be scanned simultaneously by the system.
The LABSCAN automatically creates summary reports of the results. Thanks to the MULTI display, the user can easily access a range of analysis reports. To ensure complete quality control, the system has an angle adjustment mechanism that allows the user to position the test sample at any installation angle.
Alongside LABSCAN, vehicle glass manufacturers can also benefit from ISRA’s SCREENSCAN-Faultfinder. This sister system enables inline measurements at the same performance levels, and allows the results from Carglass® (LABSCAN) and the glass manufacturers (SCREENSCAN) to be compared with just a few clicks, ensuring full transparency in processes and quality.