For over 60 years and now in its third generation, Glas Berger from Viehdorf near Amstetten, Austria, has been a recognized specialist for interior glass and curved safety glass. With 30 employees, diverse glass projects are implemented on a 4,000 square metre production area.
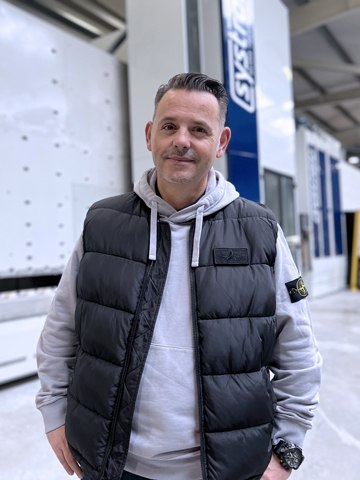
The company handles everything from construction to assembly. Managing director Erwin Berger said, “Our company is designed as a single-shift production and we process around 40,000 square metres of glass per year. Our main focus is on high-quality glass for interiors, but canopies, parapets and outdoor garden fences are also becoming increasingly important.
“The systron proHD glass processing centre with waterjet and the systron storage solution are our centrepieces. The machine continues to run during the lunch break, the proHD operator can always help out with other machines and when he goes home, another third of a shift can work on unattended. For the unmanned shift, we mainly buffer more complex panes, such as shower doors with several cut-outs.”
Waterjet cutting has become indispensable
The possibility of producing glass cut-outs with a waterjet was new for Berger. “Waterjet cutting is an extremely flexible and gentle way to cut glass. You can cut radii with just 2 millimetres and the quality is very good. You no longer have to seam anything because the waterjet cut is so tension-free.
“The milling cutter creates a lot more tension and micro-cracks in the glass, which means you can’t temper it directly. The maintenance of the waterjet unit is manageable, the nozzles have to be serviced again and again, but in relation to the drills, this is negligible.”
The vision of the Lower Austrian glass refiner was a fully automatic grinding and processing centre with little maintenance, easy to operate and with top service. The systron proHD with 20-slot storage system can absolutely meet these requirements.