Growth and development in the pharma industry combined with the stress related to the worldwide pandemic emergency has pushed the entire sector into an overproduction of hydrolytic Class I neutral glass pharma containers, such as vials, ampoules, and syringes.
![]() | ![]() |
The global demand for glass is quickly increasing and, therefore, requires the installation of a number of new plants worldwide.
Glass Service Italy is assisting its clients in meeting this increasing demand by designing furnaces optimised with Danner or Vello technology for the production of hydrolytic Class I pharmaceutical glass containers, and installs them all over the world.
To date, GS Italy has installed 14 furnaces in Belarus, Iran, China, Russia, Pakistan, and India.
CRITICAL PARAMETERS FOR PHARMACEUTICAL GLASS
Pharmaceutical glass production, with glass batch based on boron content, has the following critical points:
- high melting temperature, 1600°C;
- elevated boron evaporation from the batch, leading to a high corrosion rate in chimney and waste ducts, and production of silica salt knots in the glass;
- increased viscosity of glass;
- greater energy consumption;
- instability of glass quality;
- greater risk for batch pollution.
These issues, combined with the demand for high quality glass, require specialised furnace design that allows for correct production and stability in glass quality.
MARKET REQUIREMENTS FOR FURNACE PERFORMANCE
Stability of production
Every year an increased demand is reported for both quantity and quality from glass tube producers. Currently, standards are requesting for glass tubes with increased stability in:
- OD (outer diameter) and ID (inner diameter);
- TH (thickness);
- bending;
- absence of bubbles and air lines;
- absence of stones;
- stability of batch and chemical/physical characteristics.
To achieve this high stability performance, full control over the melting process and the forming process is required.
To that end, furnace design should be tested in several applications and over long-term operation. Correct design of the electric booster system, bubblers, and all the furnace equipment, as well as the furnace design for melting and forehearth, are very important for good production and stable quality.
Low energy consumption
GS furnaces are low consumption units, meeting the market requirements for reduction in both cost and CO2 footprint. The preferred fuel is natural gas and oxygen because the furnace is a high temperature unit (1600°C). The use of natural gas and preheated air is also possible, as well as HFO and preheated air, but is not recommended due to energy consumption.
In several oxy/gas 20 TPD (N.2 Danner line) installations, GS furnaces have already achieved the targeted energy consumption of 1250 Kcal/kg fossil + 0.46 KWh/kg electric booster.
Long-term operation
Correct design combined with the correct refractory material can ensure a four-year run for the furnace melting area and forehearth.
Achieving this level of performance requires accurately engineered: refractory design, burner design and positioning, booster electrode position, water cooled bubbler tubes, temperature management, special throat cooling technology, and special side cooling technology. After a four-year run, 65 per cent of AZS and refractory materials should be changed, while the steel structure and equipment can be used for a second run.

Easy maintenance and management
Easy maintenance is quite important for four-year glass production stability and GS furnaces are designed for this scope because the furnace and its equipment require very low maintenance. This includes several solutions for cleaning the burners and unclogging the bubbler that require very little maintenance time as all these activities can be done while the furnace is in production.
GLASS SERVICE SOLUTIONS
GS furnaces have a number of special solutions regarding refractories as well as for complete design. These special solutions guarantee glass quality and stability, low energy consumption and a four-year run. GS has designed Danner furnaces with two or four lines and Vello furnaces with two lines. Standard sizes are 20 TPD pull for Danner furnaces with two lines, 40 TPD pull for Danner furnaces with four lines, and 32 TPD pull for Vello furnaces with two lines (pull is limited by the speed of the tube cutting device).
GS has also developed some unique equipment the furnace refractory design.
Special batch chargers
Batch charger devices have a fundamental role in the melting process. The combination of the batch charger machine and the batch charger-area furnace design should guarantee low dust in the chimney, low boron evaporation, high machine life, stability of glass level, and correct batch distribution in the melting area.
GS has developed a special machine design coupled with the furnace batch charger area. The machines are screw-type batch chargers and can operate in 2-, 3- or 4 units, according to furnace size and pull. Batch charging screw rotation speed and charger ton/h rate are automatically managed by the process control system. Moreover, the batch charger machine has been engineered to have complete electrical insulation from the supporting structure.
Special bubblers
Bubblers fundamentally affect glass quality and furnace life. Expert design and positioning of bubblers are essential to avoid long term issues. An error in bubbler positioning could result in poor glass quality, while bad bubbler design may result in bottom drilling, reducing the life of the furnace bottom to only one year. With bottom temperatures reaching as high as 1550°C in this furnace, bottom corrosion is a very real issue.
Aiming to produce better quality glass and extend furnace lifetimes, Glass Service has engineered solutions to meet these industry-wide needs. To address the devastating effects of high bottom temperatures, GS has developed water-cooled bubbler tubes designed to reduce the AZS bottom temperature in the bubbler area and avoid the corrosion of bubbler tubes AZS bottom blocks.
GS has also developed constant flow technology for the bubbler device; this technology can guarantee a constant flow rate in the event of bubbler tube nozzle clogging. Additionally, in the case of irreversible clogging, the water-cooling bubbler tubes can be easily changed while in operation. The bubbler can also operate in both oxygen (recommended) or compressed air. These innovations should guarantee a continued bubbling service for the entire furnace life.
Special molybdenum electrodes holder
Electrode holders also require specialised design and cooling due to high temperatures (1550°C) in the furnace bottom. GS has developed its own molybdenum electrode holders with a strong, high-temperature resistant cooling head, and integrated double high efficiency cooling technology + compressed air.
The high-temperature, stress resistant head allows the electrode holders to operate at very high temperatures. Meanwhile, the use of high cooling rate water technology reduces the temperature of the electrode AZS block, avoiding glass leakage and block corrosion. The double cooling (water and air) electrode holders can be used separately; with water during normal operation; and with air in emergency conditions.
Special burners and burner oxy-gas skids
Oxy-gas burners have a special role in the borosilicate glass melting process, they have to guarantee: correct flame pattern distribution, low boron evaporation from glass surface, and easy maintenance.
GS oxy-gas burners, their size, their number, their position in the combustion chamber, and the burner blocks are designed as one unique system. The burners also have double impulse technology allowing for adjustable flame length.
Burner skids and gas/oxy rate stability are two of the most important devices for borosilicate furnaces. The combustion skid should guarantee the correct combustion ratio of natural gas and oxygen. The melting process and the redox value of the batch, as well as boron evaporation, are very sensitive to the stability of this parameter.
GS developed the skid as a standard unit, each controlling three burners sections with independent flow control for natural gas and oxygen. The flow control has a high accuracy rate integrated with mass flow calculation for both gases. The design also includes a compressed air section to cool burner nozzles in the case of a shut-down due to maintenance or an emergency.
Process control system
The process control system allows real-time monitoring of: high precision temperature reading, stability of process control loops, high precision in mass flow control, advance capability calculation, trend advanced management for all process variables, management of historical and real time alarms, easy and intuitive HMI (Human Machine Interface), and main loop redundancy for emergency control in case of a DCS failure.
Performance of these functions is managed by the DCS HC900 Edge from Honeywell with integrated PC Scada Citec with double screen (single or multiple PCs) and two local displays; a group of P108 Eurotherm instruments is installed for redundancy.
The process control system also manages all the furnace machines: batch chargers, glass level, bubblers, electric boosters, combustion, furnace pressure control, cooling, etc.
All machine controls and control loops are integrated into a single process control system. With this solution, the advanced and integrated furnace process control strategy is managed as a whole.
Strict safety protocols are in place for operators and furnaces in the event of an emergency, including restarting after a black-out. Additionally, the SIL2 capability safety level has been designed to meet EU and USA market standards.
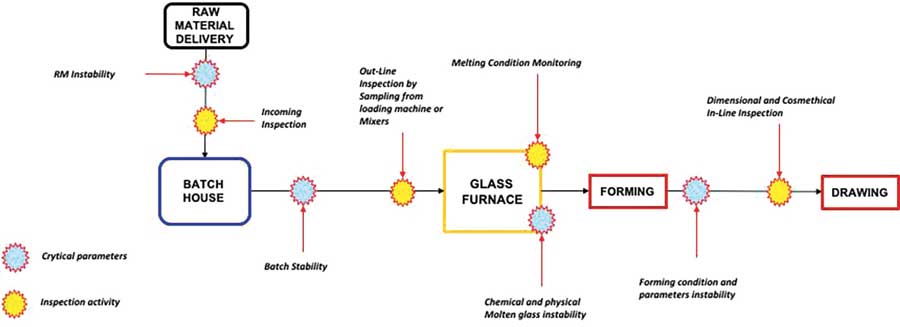
Full process control procedure
Any mismanagement of raw materials or melting conditions can introduce persistent defects in the glass. Glass quality can only be guaranteed if there is strict control over the entire production process. As such, training is an integral part of GS customer service process.
To ensure customers are fully trained in process control procedure, GS has assembled a team of specialists with many years experience working with borosilicate glass tube hydrolytic class I glass.
GS training services include: assessing the actual status of customers’ internal procedures, training on quality control procedures, ranging from raw materials to final products, and training on chemical and physical laboratory tests and procedures.
CONCLUSION
Glass Service Italy, with more than 14 fully successful installations worldwide, is the only furnace manufacturer with long-term experience in borosilicate pharmaceutical glass tubing hydrolytic class I (alfa 50).
GS designs specialised equipment/machines and technology for these unique furnaces, engineered for low energy consumption and minimal maintenance.
GS is also able to provide technological training as part of customer service, ensuring high quality support and excellent success rates.
Glass Service Srl
www.glassservice.it